CrazyTalkSVT
Veteran CEG'er
I started this project a little over a year ago and have been dragging my butt on it ever since. Finally made some pretty good headway.
I'm lacking in the "stock photos" department so these first couple I had to borrow.
This is from Tousley and we are looking at the #4 bar in which the sway bar bolts to:
I borrowed this from KyleQ (put my own arrows on):
Some how it has become "the norm" to just apply boxing plates to the bottom of these arms. This is a huge waste of time if you end the boxing plate right at the end tabs. If you have knowledge of stress risers or stress concentration you can understand the simple concept.
So why redesign the arm completely?
Coming from a stock setup side, it doesn't make a whole lot of sense. From a performance side or air ride side it makes tons more sense. Safety was a major concern of mine. Airing my car up and down puts my suspension through a very broad range of motion. It becomes drastic one way (up) and drastic the opposite way (down). There is no way around it...it's the nature of the beast.
So, the rear sway bar attaches to these arms and through the chassis range of motion, the sway bar has to articulate in conjuction with the arm. The bushing(#15) design between the sway bar dog bone(#14) was not designed to take up that much range. Because of the bushing maxing out and still having more distance up/down to contend with, the sway bar starts to pull/twist on that stock lateral arm.
The fear of the bar being twisted one way only to be pulled and twisted the other way puts the yield strength of the arm in jeopardy. So until I get these arms done, there is no rear sway bar for me.
Design picture:
This is the prototype which allowed me to mock-up for clearance issues and check for any binding:
Then we have the money load :laugh::
This is as far as I am now. The bars are fully polished and need to be sent off to be clear anodized. I misplaced my new dog bones that I bought from Tousley. I need to track them down or buy new ones again. DOH! :blackeye: Then hopefully I will have some assembled pictures. Until then, have a good 4th!
Cheers!
I'm lacking in the "stock photos" department so these first couple I had to borrow.
This is from Tousley and we are looking at the #4 bar in which the sway bar bolts to:
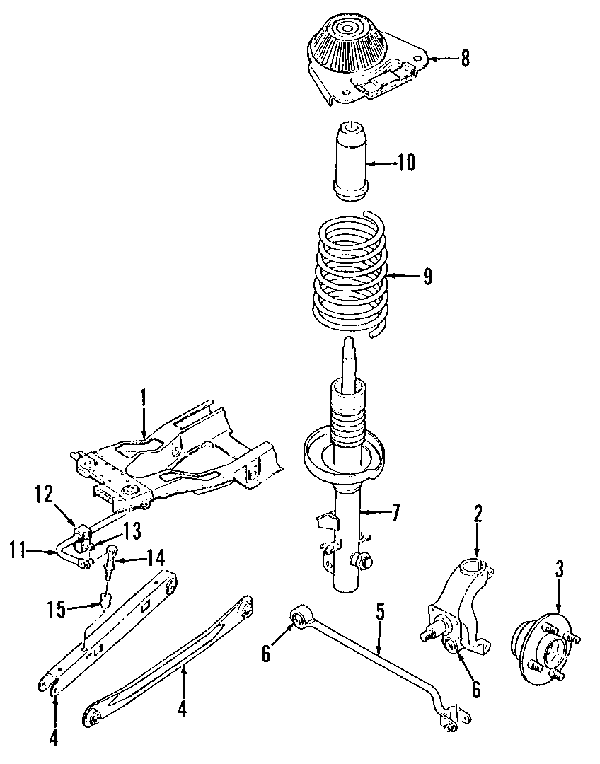
I borrowed this from KyleQ (put my own arrows on):
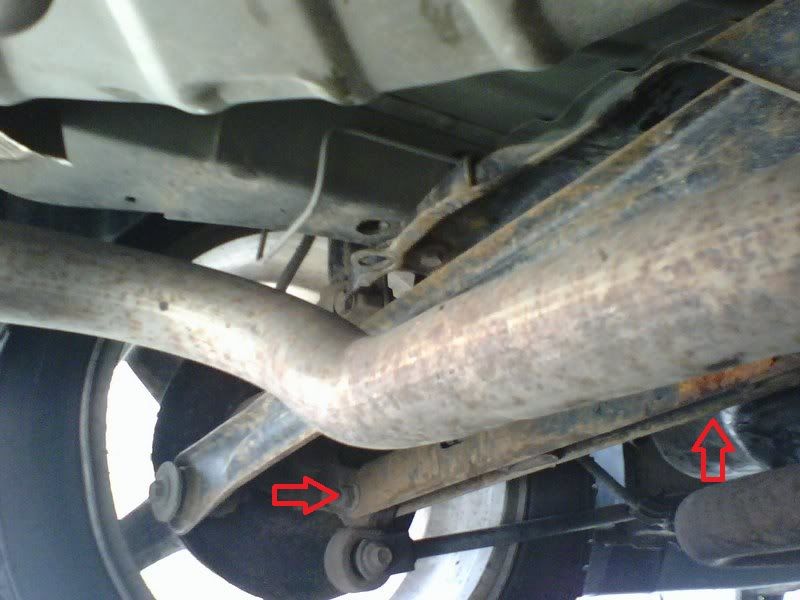
Some how it has become "the norm" to just apply boxing plates to the bottom of these arms. This is a huge waste of time if you end the boxing plate right at the end tabs. If you have knowledge of stress risers or stress concentration you can understand the simple concept.
So why redesign the arm completely?
Coming from a stock setup side, it doesn't make a whole lot of sense. From a performance side or air ride side it makes tons more sense. Safety was a major concern of mine. Airing my car up and down puts my suspension through a very broad range of motion. It becomes drastic one way (up) and drastic the opposite way (down). There is no way around it...it's the nature of the beast.
So, the rear sway bar attaches to these arms and through the chassis range of motion, the sway bar has to articulate in conjuction with the arm. The bushing(#15) design between the sway bar dog bone(#14) was not designed to take up that much range. Because of the bushing maxing out and still having more distance up/down to contend with, the sway bar starts to pull/twist on that stock lateral arm.
The fear of the bar being twisted one way only to be pulled and twisted the other way puts the yield strength of the arm in jeopardy. So until I get these arms done, there is no rear sway bar for me.
Design picture:
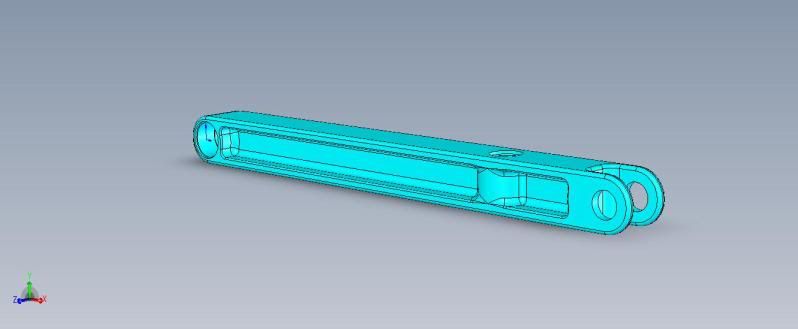
This is the prototype which allowed me to mock-up for clearance issues and check for any binding:
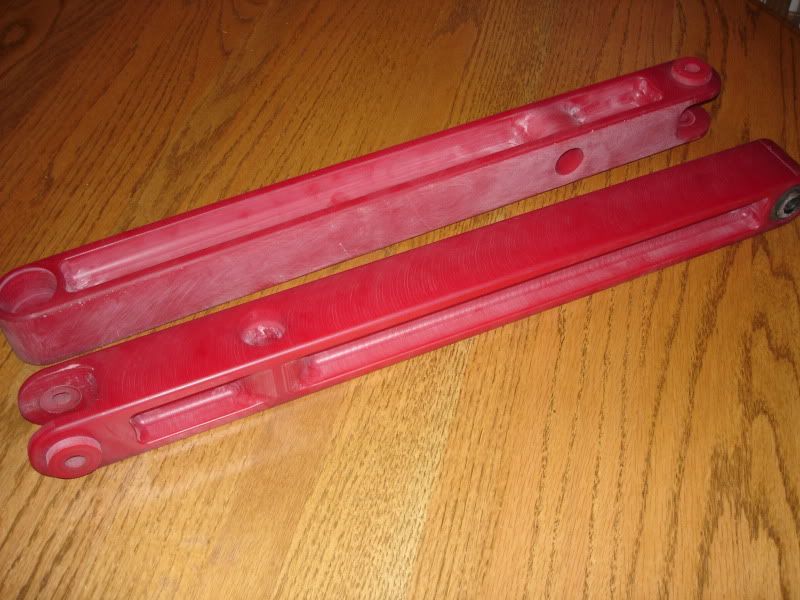
Then we have the money load :laugh::
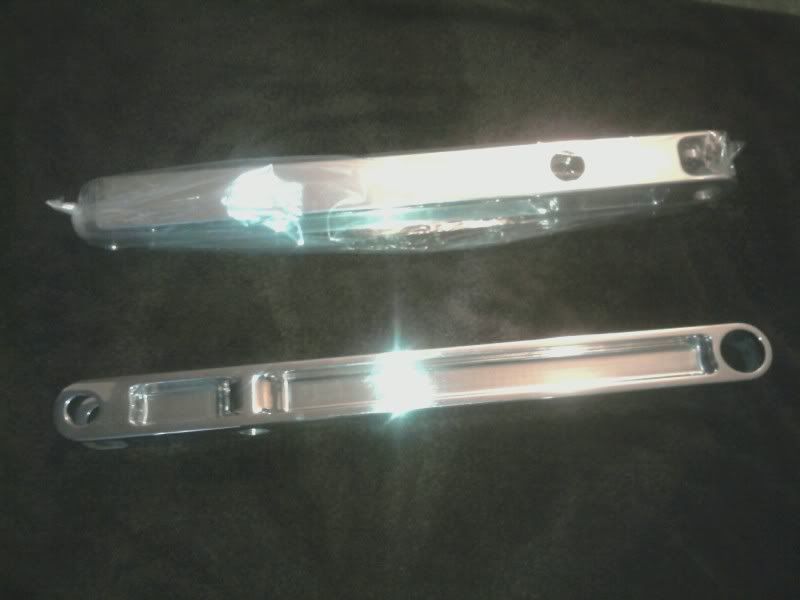
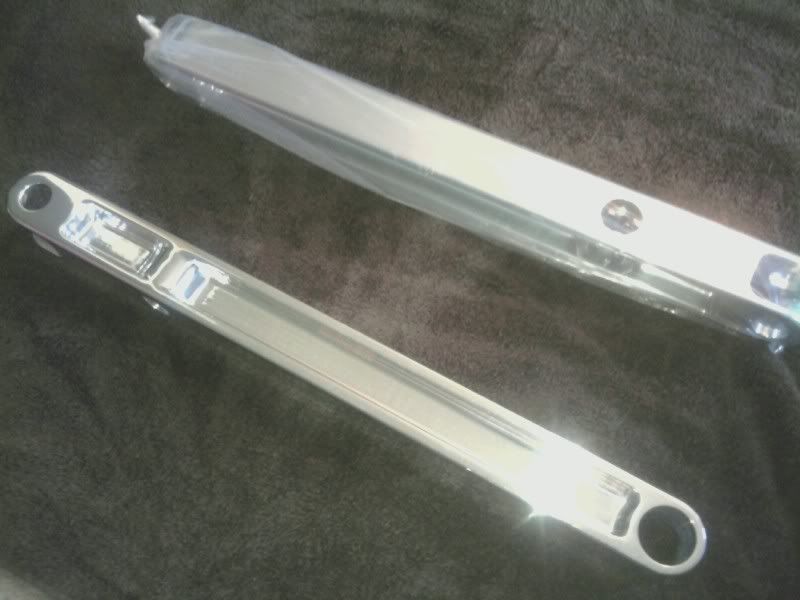
This is as far as I am now. The bars are fully polished and need to be sent off to be clear anodized. I misplaced my new dog bones that I bought from Tousley. I need to track them down or buy new ones again. DOH! :blackeye: Then hopefully I will have some assembled pictures. Until then, have a good 4th!
Cheers!